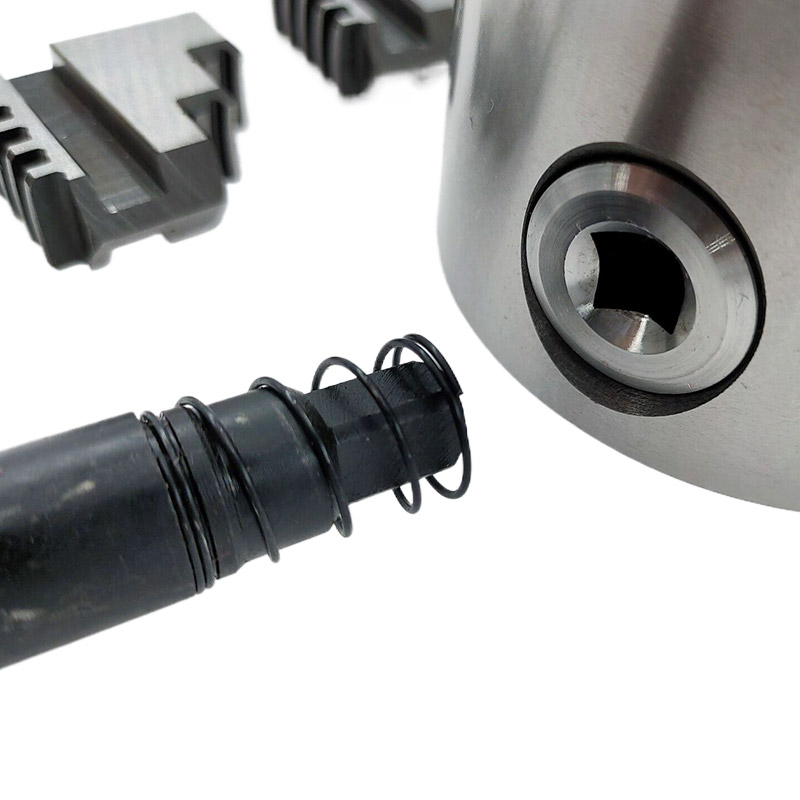
Power of Metal Lathes: Metal Lathe Projects
Introduction
In the realm of metalworking, metal lathes stand as indispensable tools, capable of transforming raw metal blocks into intricate and functional components. Whether you’re a seasoned machinist or an aspiring metalworker, metal lathe projects offer an avenue to unleash creativity, hone skills, and produce valuable items for various applications in 2024.
Understanding Creative Metal Lathe Projects and Their Capabilities
Metal lathes are machines that rotate a metal workpiece, allowing a cutting tool to shape it into desired forms. They primarily function to create cylindrical or conical shapes, with the ability to perform various operations, including:
-
Turning: Removing material from the workpiece to create a smooth, rounded surface.
-
Facing: Flattening the end of a workpiece perpendicular to its axis.
-
Boring: Enlarging an existing hole or creating a new one within the workpiece.
-
Threading: Cutting helical grooves onto the workpiece to create a screw-like pattern.
-
Parting: Separating a workpiece into two distinct pieces along a defined line.
Essential Metal Lathe Tools and Accessories
To embark on your metal lathe projects, you’ll need a basic set of tools and accessories:
-
Three-Jaw Chuck: A versatile chuck for securing round workpieces of various sizes.
-
Four-Jaw Chuck: Ideal for holding irregularly shaped workpieces or those requiring more precise alignment.
-
Cutting Tools: A variety of high-speed steel (HSS) or carbide cutting tools for different turning, facing, boring, threading, and parting operations.
-
Tool Rest: A support for the cutting tool, ensuring precise control and stability during operation.
-
Measuring Tools: Calipers, micrometers, and gauges for accurate measurement and dimension control.
-
Safety Gear: Protective glasses, gloves, and a dust mask to safeguard yourself from hazards.
Types of Metal Lathes and Their Applications
Metal lathes come in various types, each suited for specific purposes:
-
Engine Lathes: The most common type, offering a versatile range of operations and suitable for both beginner and advanced projects.
-
Mini Lathes: Compact and portable, ideal for small-scale projects and hobbyists with limited workspace.
-
CNC Lathes: Computer Numerical Control (CNC) lathes provide high precision and automation for complex projects and mass production.
Choosing the Right Metal Lathe Project
When selecting a metal lathe project, consider your skill level, available tools, and desired outcome. Start with simple projects like bushings or spacers to gain confidence, then progress to more complex tasks like threading or gear cutting.
Safety Guidelines for Metal Lathe Operations
Safety is paramount when working on a metal lathe. Always follow these guidelines:
-
Secure the workpiece: Ensure the workpiece is firmly mounted in the chuck or between centers to prevent accidents.
-
Maintain proper posture: Stand with a balanced stance, knees slightly bent, and keep your hands away from rotating parts.
-
Wear appropriate PPE: Use protective glasses, gloves, and a dust mask to shield yourself from hazards.
-
Never operate the lathe while impaired: Avoid operating the lathe while under the influence of alcohol or drugs.
-
Stay alert and focused: Maintain full attention on the task at hand and avoid distractions while operating the lathe.
Basic Metal Lathe Operations for Beginners
Start with these fundamental metal lathe operations to master the basics:
-
Rough Turning: Initial shaping of the workpiece to remove excess material and establish the desired form.
-
Smoothing: Refining the surface of the workpiece to eliminate irregularities and achieve a smooth finish.
-
Detailing: Adding intricate details, such as grooves, ridges, or decorative elements, to enhance the appearance.
-
Polishing: Using abrasive compounds and polishing wheels to achieve a shiny, mirror-like finish.
Intermediate Metal Lathe Projects to Elevate Your Skills
Once you’ve mastered the basics, venture into these intermediate projects:
-
Creating a Bolt: Combine turning, facing, and threading operations to produce a functional bolt.
-
Turning a Sleeve: Shape a precise sleeve with a smooth bore and outer diameter.
-
Cutting a Taper: Learn the technique of creating a tapered form on the workpiece.
-
Making a Tool Holder: Turn a custom tool holder to organize and securely store your lathe tools.
Advanced Metal Lathe Projects for Experienced Machinists
For experienced machinists, these projects offer a challenge:
-
Turning a Gear: Produce a functional gear with precise teeth and accurate dimensions.
-
Machining a Knuckle Joint: Create a complex knuckle joint with multiple moving parts and intricate details.
-
Threading a Pipe Fitting: Master the process of threading a pipe fitting for plumbing applications.
- Making a Custom Lathe Chuck: Design and turn a custom lathe chuck for specific workpiece holding needs.
Maintaining Your Metal Lathe for Optimal Performance
Just like any tool, proper care is crucial to ensure your metal lathe’s longevity and optimal performance. Here are some maintenance practices:
- Cleaning and Lubrication: Regularly clean your lathe to remove metal chips, dust buildup, and coolant residue. Follow the manufacturer’s instructions for lubricating moving parts to prevent friction and wear.
- Sharpening Cutting Tools: Maintain sharp cutting tools for efficient and clean cuts. Learn how to sharpen your HSS or carbide tools using appropriate sharpening stones or invest in a sharpening jig.
- Tool Maintenance: Regularly inspect your cutting tools for damage, such as chipped edges or worn tips. Replace or recondition damaged tools to ensure proper operation and safety.
- Coolant System Maintenance: If your lathe utilizes a coolant system, maintain proper coolant levels and cleanliness to prevent overheating and extend tool life.
Advanced Safety Techniques for Experienced Metalworkers
As you progress in your metal lathe projects, consider incorporating these advanced safety techniques:
- Using Live Centers and Dead Centers: Learn the proper use of live centers and dead centers for longer workpieces and ensuring precise alignment during turning operations.
- Cutting Speeds and Feeds: Understand the concept of cutting speeds and feeds, selecting appropriate settings based on the material being machined and the desired outcome.
- Advanced Workholding Techniques: With experience, explore advanced workholding techniques like chucking techniques, using centers, and mandrels for specific workpiece shapes.
- Chip Control: Implement strategies for safe and efficient chip control to prevent chip accumulation in the work area and potential injuries.
The Basics of Metal Lathe Operations
Before delving into specific projects, it’s essential to understand the fundamentals of operating a metal lathe. A metal lathe is a machine tool used to shape metal, wood, or other materials by rotating the workpiece against cutting tools. The lathe’s spindle holds the workpiece, while various tools, such as cutting tools and drill bits, are used to shape and refine it. Mastery of lathe operations involves understanding spindle speed, feed rates, tool selection, and precise measurements—a blend of artistry and technical proficiency.
Crafting Precision Components: Turning and Facing
One of the most fundamental projects on a metal lathe is turning and facing. Turning involves rotating a cylindrical workpiece against a stationary cutting tool to create cylindrical shapes, such as shafts or pins. Facing, on the other hand, is the process of cutting a flat surface perpendicular to the axis of rotation. These techniques are foundational in machining and are essential for creating precise components used in various industries, from automotive to aerospace.
Creating Threads: Tapping into Functional Precision
Threads are integral to many mechanical assemblies, providing the means to secure parts together or adjust components. Metal lathes are indispensable for cutting threads, whether external or internal, using threading tools and dies. Projects involving thread cutting showcase the lathe’s ability to achieve high accuracy and repeatability, crucial for manufacturing threaded parts like bolts, nuts, and threaded rods.
Precision Boring: Enhancing Fit and Function
Boring operations on a metal lathe involve enlarging existing holes or creating precise internal diameters. This technique is vital for achieving accurate fits in mechanical assemblies, where tolerances are critical. Boring tools, such as single-point cutters or boring bars, allow machinists to achieve smooth, concentric bores that meet exact specifications. Projects involving boring highlight the lathe’s capability to refine and enhance the functionality of machined parts.
Turning Complex Shapes: From Cones to Eccentrics
Beyond simple cylindrical shapes, metal lathes excel at turning complex geometries, such as cones, spheres, and eccentric shafts. These projects require advanced techniques, including taper turning and eccentric turning, which involve adjusting the lathe’s setup to achieve non-linear profiles or varying diameters along the workpiece. Such projects not only demonstrate the lathe’s versatility but also challenge machinists to hone their skills in geometrical precision and creative problem-solving.
Restoring Vintage Machinery: Preserving Heritage with Precision
Restoration projects involving vintage machinery showcase the ultimate fusion of craftsmanship and historical preservation. Metal lathes play a crucial role in restoring worn or damaged parts of antique engines, tools, or industrial equipment. Machinists meticulously replicate original components, ensuring historical accuracy while rejuvenating functionality. These projects highlight the enduring value of metal lathes in maintaining and honoring industrial heritage.
Custom Tooling: Tailoring Solutions for Specific Needs
In many manufacturing settings, custom tooling is essential for optimizing production processes and overcoming unique challenges. Metal lathes empower machinists to fabricate custom tools, jigs, and fixtures tailored to specific manufacturing requirements. Whether it’s designing precision gauges, cutting tools, or production molds, the ability to create bespoke tooling enhances efficiency and quality in industrial applications. These projects underscore the adaptability and innovation facilitated by metal lathe technology.
Artistic Expressions: Sculpting Metal with Precision
Metalworking is not solely confined to functional components; it is also a form of artistic expression. Artists and craftsmen utilize metal lathes to sculpt intricate designs, decorative elements, and artistic forms from metal. These projects transcend traditional machining techniques, blending technical skill with creative vision to produce aesthetically pleasing and culturally significant artworks. Metal lathe artistry exemplifies the fusion of craftsmanship, innovation, and artistic ingenuity.
The Future of Metal Lathe Technology
The realm of metal lathe technology is constantly evolving, offering exciting advancements for machinists of all levels. Here’s a glimpse into what the future holds:
-
CNC Lathes with Advanced Functions: CNC lathes with even more sophisticated programming capabilities will enable complex machining with increased precision and automation.
-
Advanced Tooling Materials: New cutting tool materials with extended life and improved performance will enhance efficiency and reduce production costs.
-
Automated Safety Features: Lathes may incorporate advanced safety features like automatic shut-off mechanisms, chip ejection systems, and laser alignment tools.
-
Integration with 3D Printing: Potential integration with 3D printing technologies could offer new possibilities for rapid prototyping and hybrid manufacturing processes.
These advancements point towards a future where metal lathes become even more versatile, efficient, and safe, empowering machinists to bring their creations to life with unparalleled accuracy and sophistication.